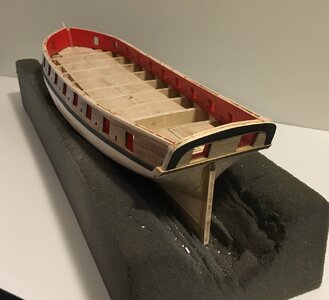
The painted bulwarks certainly change the look of the model. Now I’m looking ahead to coppering the hull. Firstly, a stamping jig had to be made as described in the kit supplied manual.
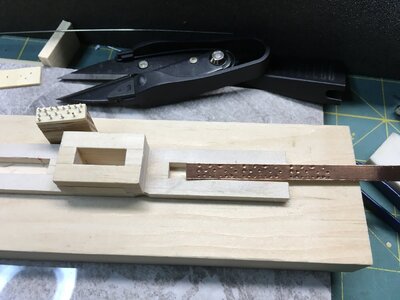
Once the jig is made the stamping process is simple. Hit it with a hammer

The size of nails for copper sheathing is given by Goodwin at 5/16” and Mondfeld at 3/8” to 1 1/4”. That equates to a range of 0.005” to 0.02” at 1/64 scale. The smaller size makes me think it’s not worth trying to replicate but possibly the 0.02” is.
My first attempt at making the stamp involved a piece of pine with tiny nails. I clipped of the nail heads but had a hard time getting all the protrusions dead flat and to the same height. When striking the stamp to emboss the tape I found the nail stubs sunk randomly but slightly into the soft pine. That changed the evenness of the pattern depth but the nails were too big anyway so that got tossed. Then I tried some oak with nails. Same issues so that got tossed. Next was more research.
I had some rigid 0.025” steel wire in a parts box so time to experiment, again.
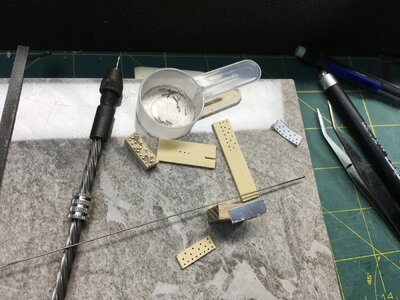
This time I laid two pieces of 1/16” yellow cedar together and hand drilled holes with a 0.025” bit. I took my wire and using a Dremel ground the end flat. Using a perfectly flat kitchen tile on the bench I placed the ground flat end of the wire into the double layered cedar. (My wife will possibly notice the new rectangular hole in the tiled kitchen wall but it’s for a good cause

Using snips I cut the wire as close to the top piece of cedar as possible. Filed that end flat and removed the by now 1/8” long piece of wire. Repeated that many times, lost pieces, crawled around the floor, said bad words and made more. Those 1/8” lengths of wire were then glued into an exact sized 1/16” thick piece of cedar. This is the head of the stamp.
Anticipating a repeat problem of my new wire “nails” sinking into the base of the wood stamp I needed another solution. I thought a very thin metal plate between the bottom of the nails and the stamp base would keep the new nails consistent. By the time they are hit multiple times I expected they might shift.
Where to find really thin metal plate? Cast your minds back to the 80’s and 90’s and you will no doubt remember the 3.5” floppy computer discs. If you take one apart the sliding piece of metal (see photo below) becomes a source of very thin mini metal plates.
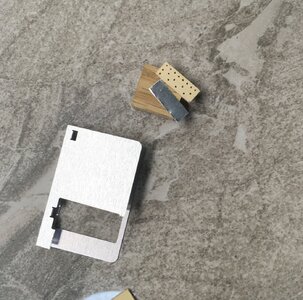
I cut, then sandwiched, a metal plate between the stamp nail head and main body. Superglue worked. Time to experiment, again.
The tape embossing works but it takes trial and error to get consistency. Hit it too hard and the tape crinkles, too soft and the embossing is erratic. I think this will work for me but it’s going to be a long process. I have yet to get the copper tape off the paper backing cleanly but that’s for later.
I wonder if the vacation photos on the now destroyed 3.5” floppy disc will be missed? The kitchen tile will be

Last edited: