Meanwhile... (this what I call in-between the main build). I thought it would be interesting to change the routine, I would still need to do it for the kit so...
Here is the part from the internal hull section, which we will be building next year. The pump well and shot locker. Below is the image for reference from the AOTS book. This is an isometric projection in scale 1:48. I think, the image definitely has some flaws, take a look at the door from the pump well. How will it open, unless it opens 'inside'?
I will show the pump well assembly from the kit once we get to this point, today, just for fun a will show this little project a cratch build pump well. This will include woodwork and metalsmith. The idea to make functional doors and show nails.
I took the templates from our kit and compared them to plans from the book, and come on with my own design. I use SwissPear and Pearwood as the main timber.
Then, I build sides. Each plank is 3mm wide, the same as from our kit. 0.23mm drill bit used to make holes for future nails (30 gouges brass wire, about 0.24mm)

Next, all the internal dividers and glue everything together. To imitate nails a brass wire was inserted and cut flush.
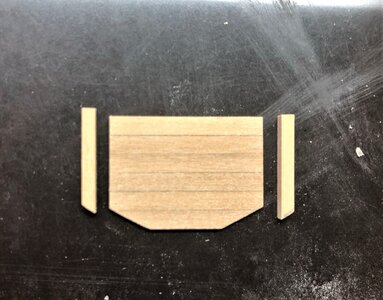
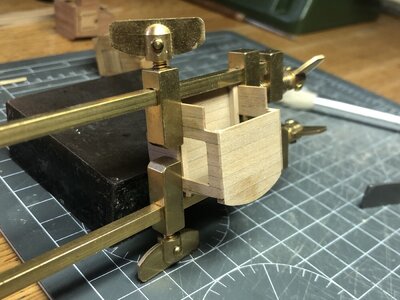
A much more exciting and at the same time challenging work was the metalsmith- making hinges. A strip brass 0.9mm wide and 0.3mm thick predrilled using the mill and 0.25mm drill bit. This time I achieved better results (I think

) compared to my test, the holes are straight, for the most part.
1mm brass tubing cut into small pieces, then I will solder to this strip to make individuals hinges. I made the jig to make all the cut pieces the same
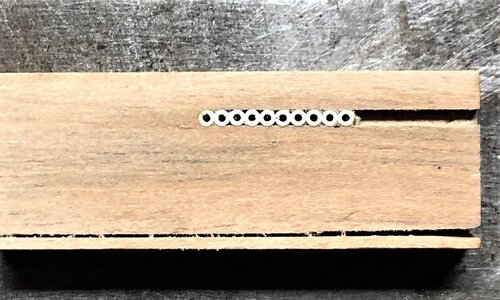
Here is the part ready to solder
Knuckle made from the same tubing, but before it cut for pieces the 0.3mm hole made.

Once the hole drilled, the part cut to the same length as the hinge. The knuckle assembled by soldering a pin and knuckle holder together.
Parts were trimmed to the required size, the ends of the pins were rounded using cup bur. All parts where blackened using 'Brass Black'
Assembly the pump well and shot locker was the most fun. I re-do twice as I didn't like it. Below is the first variant. Macro reviled all the blemish and mistakes. Why the hinge too short and the bolts go between the planks? Well, no answer but re-do.
A much better variant, but still is not up to my acceptance level (on the right side the old one, on the left is the new one)
This is the one I like the most!
Both doors in action.
Well... since there so many mistakes were made during construction a Supervisor was called to maintain and monitor the further Alert assembly, He starts his job immediately before the New Year, His first assignment was a completed pump well and shot locket built from scratch.
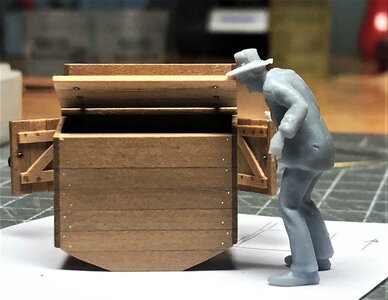